4 minute read
The transformational benefits of working together
The transport sector must reduce CO2 emissions to meet the UK's net-zero target by 2050. The fact that consumers are voting with their feet when it comes to sustainability, according to a McKinsey study, makes this goal even more compelling.
Collaboration, through shared resources and optimised fleets, can help achieve these goals, cutting costs and emissions. This is echoed in Wincanton’s survey results which show that 83% of businesses surveyed say that optimising the carbon footprint of logistics is key to achieving their goals in this area. But are you aware of the full benefits of collaboration to your business?
Clue: it’s not just about net-zero.
Benefits of shared logistics resources and fleet collaboration
Cost reduction
Sharing logistics resources reduces empty runs and optimises load capacities, lowering fuel consumption and operational costs. Wincanton's research shows 37% of organisations have already seen cost reductions from collaborative efforts.
Environmental impact
Fleet sharing reduces the number of vehicles on the road, cutting CO2 emissions. Wincanton's EyeQ solution has helped businesses achieve up to 10% reduction in emissions through optimised transport activities.
Enhanced efficiency and resilience
Collaboration provides access to a broader range of resources and expertise, beneficial during peak times or when specialised vehicles are needed. Companies can scale operations based on demand, ensuring high service levels and efficiency.
Access to technology
Digital platforms like Wincanton's EyeQ offer real-time data and insights, aiding in route planning, load optimisation, and performance monitoring, contributing to sustainable transport practices.
Challenges and solutions for building effective partnerships
Our survey results tell us that there are barriers that prevent collaboration, with over a third (38%) finding it difficult to find the right partner to collaborate with.
Collaboration is only possible through strong partnerships – not just a supply chain partner, but other actors along the supply chain, for example, FMCG and grocery brands, and even, potentially, competitors. What are the steps businesses can take to build a mutually beneficial partnership?
Finding the right partners
Identifying partners with similar values and goals is crucial. Digital platforms can aid in vetting potential collaborators, establishing effective partnerships.
Meeting service level agreements (SLAs)
Clear SLAs ensure all parties meet their obligations. Regular monitoring and communication help maintain service quality in collaborations.
IT systems and security
Integrating IT systems and ensuring data security are key concerns. Secure platforms like Wincanton’s EyeQ facilitate safe data sharing and collaboration.
Resource management
Managing a network of collaborators requires dedicated teams and technology to automate processes, reducing administrative burden and improving efficiency.
Conclusion
We believe the best supply chains are collaborative.
If we’re really going to bridge the net-zero challenge, and optimise costs, then the answer is for like-minded organisations to share resources, using class-leading technology to enable collaboration. This way we can reduce the number of dead miles or wasted journeys carried out, benefitting not just the bottom line, but the planet too.
Download our latest guide to learn more about how to achieve your sustainability and operational goals.
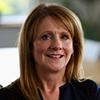
About the Author: Helen Flanagan
Product Director - EyeQ
Helen Flanagan is the product lead for EyeQ, Wincanton's digital transport control tower product. She joined Wincanton in 2023 and plays a key role in the strategic shift in the business to focus on transport services powered by digital technology. Helen brings a depth of experience in logistics operations, sales, solutions design and consulting and has enjoyed varied roles at DHL Supply Chain and Kuehne & Nagel.